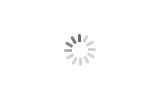
Машина для литья под давлением с горячей камерой прессования 200/300/400 тонн
марка :Daseon
Происхождение продукта :Китай
Срок поставки :30 дней
Машина для литья под давлением Умный Кастинг Машина сочетает в себе передовые технологии автоматизации и удобную конструкцию, что снижает сложность эксплуатации и обеспечивает максимальную безопасность и гибкость.
Автоматизированная система литья под высоким давлением переопределяет современное производство, объединяя передовую автоматизацию, безопасность оператора и гибкие конфигурации. Разработанная для отраслей, требующих быстрой адаптации, таких как автомобилестроение, аэрокосмическая промышленность и производство бытовой электроники, эта система оптимизирует рабочие процессы, обеспечивая точность и соответствие мировым стандартам. Ниже мы рассмотрим ее технологические инновации, ориентированный на пользователя дизайн и влияние на реальный мир.
1. Расширенная автоматизация для точного производства
The Автоматизированная система литья под высоким давлением использует передовые технологии для минимизации человеческого вмешательства и максимальной повторяемости.
Унифицированный интерфейс управления:
Сенсорный экран обеспечивает интуитивный доступ ко всем параметрам, поддерживая несколько языков для глобальных операций. Предварительно загруженные профили для распространенных сплавов позволяют выполнять настройку одним щелчком, сокращая время обучения на 50%.
На панелях мониторинга в режиме реального времени отображаются такие важные показатели, как время цикла, температура пресс-формы и потребление энергии, что позволяет операторам оптимизировать процессы на лету.
Динамическое управление процессами:
Регулирование температуры в замкнутом контуре: Нагреватели с ПИД-управлением поддерживают температуру сопла и формы в пределах ±1°C, устраняя температурные несоответствия, которые приводят к таким дефектам, как пористость или деформация.
5-этапное профилирование впрыска: Регулируемые кривые давления (0–200 МПа) подходят для материалов с различной вязкостью, таких как цинковые сплавы для дверных ручек или медь для электрических разъемов.
Программируемая гибкость:
ПЛК серии Нью-Джерси от ОМРОН хранит до нескольких пользовательских рецептов, что позволяет быстро переключаться между партиями продукции. Например, переключение с автомобильных тормозных суппортов на корпуса медицинских приборов занимает менее 5 минут.
Автоматическая регистрация неисправностей и анализ первопричин сокращают время устранения неполадок на 35%, а коды ошибок отображаются понятным языком.
2. Безопасность оператора и эргономичный дизайн
The Автоматизированная система литья под высоким давлением уделяет первостепенное внимание безопасности на рабочем месте без ущерба для эффективности.
Соблюдение требований безопасности при работе с низким напряжением:
Цепи управления 24 В постоянного тока соответствуют стандартам МЭК 60204-1, что исключает риск поражения электрическим током даже во влажной среде.
Кнопки аварийной остановки и световые завесы мгновенно останавливают работу в случае обнаружения несанкционированного доступа.
Эргономические улучшения:
Механизм наклона-зажима: Наклонная на 15° плита уменьшает высоту формы на 300 мм, что позволяет операторам загружать/выгружать детали, не наклоняясь и не поднимаясь.
Регулируемые рабочие станции: Дополнительные регулируемые по высоте панели управления (диапазон 700–1200 мм) подходят для операторов разного роста, снижая утомляемость во время 8-часовых смен.
Охрана окружающей среды:
Интегрированные системы вытяжки дыма (расход воздуха до 1000 м³/ч) улавливают 95% твердых частиц и паров.
3. Масштабируемые конфигурации для различных потребностей
The Автоматизированная система литья под высоким давлением адаптируется к производственным потребностям благодаря модульной конструкции и энергосберегающим опциям.
Оптимизация мощности и энергии:
Системы с двумя насосами: Стандартные для моделей RDH200F+ сдвоенные насосы обеспечивают производительность 210 л/мин для крупносерийного производства (например, более 10 000 единиц рамок для смартфонов в день).
Эффективность одного насоса: Меньшие модели (например, RDH138F) используют насосы с переменным рабочим объемом, что позволяет сократить потребление энергии на 25% в периоды низкого спроса.
Плавильные решения для устойчивого развития:
Промышленные масляные печи: Стандартные печи достигают 85% теплового КПД, что идеально подходит для регионов со строгими нормами выбросов.
Индукционная плавка: Дополнительные индукционные плавильные печи мощностью 800 кВт сокращают потери энергии на 30% и поддерживают использование переработанных материалов, что соответствует целям экономики замкнутого цикла.
Тяжелые аксессуары:
Гидравлические подъемные столы: Эти платформы упрощают обработку форм для крупных компонентов, таких как корпуса аккумуляторных батарей электромобилей.
Модульные системы распыления: Программируемые распылители наносят разделительные составы на водной основе или без растворителей, что позволяет сократить отходы материала на 20% и выбросы ЛОС на 90%.
4. Отраслевые приложения и проверка производительности
The Автоматизированная система литья под высоким давлением преуспевает во всех секторах, обеспечивая измеримую рентабельность инвестиций.
Успех потребительской электроники:
Производитель корпусов маршрутизаторов 5G добился точности размеров ±0,03 мм с помощью сервоприводной регулировки пресс-формы.
Системы рекуперации энергии позволили повторно использовать 15% гидравлической энергии, сократив выбросы углерода на 12 тонн в год.
Параметр
Краткое содержание
The Автоматизированная система литья под высоким давлением устанавливает новый стандарт для интеллектуального производства, сочетая точную автоматизацию, безопасность оператора и экологически чистые операции. Его доказанная адаптивность в автомобильной, аэрокосмической и электронной промышленности делает его важной инвестицией для производителей, стремящихся к процветанию на конкурентных рынках, ориентированных на устойчивое развитие.